Mechanical, hydraulic, electrical transmissions.
It is not very long ago that engineers had no alternative but to use mechanical drives in every situation, and there is thus a strong tendency to continue thinking only in terms of power transmission by mechanical connection; but at the present day, four possible methods of transmission are available to a machinery designer. These are the mechanical system, the hydraulic system, the pneumatic system and the electrical system. In considering the relative merits of these alternatives, the major and overriding point is that any one of the last three gives complete freedom for the functional design of a machine; this is because the transmission consists essentially of a flexible arrangement of pipe or cable between the driving and the driven members In the case of a mechanical system, however, the configuration of the machine must be such as to permit positive connection between driving and driven components. In other words, the flexibility of the hydraulic, pneumatic and electrical system allows the functional requirements of the machine to be the foremost consideration, whereas the rigidity of a mechanical system imposes severe limitations and forces a designer to think predominantly in terms of a suitable mechanical route. The second major point is that each of these three flexible systems can provide step-less speed variation over a wide range and can be stalled without damage; the latter feature is an advantage over variable-speed V-belt drives and so is the wider range of step-less variation which can be affected. On the other hand, a positive mechanical connection between components is most suitable where a precise fixed speed is required under variable load.
The efficiency of a mechanical system decreases directly with the number of components, since the losses are cumulative in a sequence of shafts, bearings, joints and gears, chains or belts. Thus, when power has to be transmitted through a complex mechanical arrangement in order to reach a certain component, the efficiency can be quite low (and the cost high). But the efficiency of an hydraulic, pneumatic or electrical drive is not affected by the relative positions of the driven member and the power source. Consider, for example, the transmission from a tractor engine to the auger of a baler: in one current design selected at random, the drive is through six pairs of gears and one V-belt, with considerable lengths of shafting, four universal joints and appropriate bearings; the efficiency will be about 75%.
Comparisons between mechanical drives and the alternative types of drive need to be made on a specific basis, because the complexity of the mechanical system is a very pertinent factor. It is false to make a general assumption that a mechanical drive is always more efficient and less costly: this is only true in the case of the more simple mechanical arrangements. The point also applies when the extent or complexity of the mechanical system is due to a large speed ratio requirement, rather than to the position of the driven member on the machine; even when a mechanical system has a higher efficiency than the equivalent non- mechanical system, the latter may actually be justified on the grounds of a number of secondary advantages —such as complete safety, low maintenance under adverse conditions, no limitations on angles of movement, and compactness etc.—or because of the freedom of design which is afforded, or the ease and range of step-less speed variation which can be effected.
Pneumatic methods of transmission are most suitable for low power and high speeds, and are of particular value where a reciprocating action is required.
Hydraulic versus electrical systems:
Essentially, both hydraulic and electrical transmission systems are very similar. The hydraulic system consists of a pump driven by an engine, or other source ot power, and supplying fluid at a known velocity and pressure through piping to an hydraulic motor; the electrical system consists of a generator driven by an engine and feeding through wiring to an electric motor elsewhere. In both cases, it is possible to effect step-less speed control, the motors have excellent torque-speed characteristics for variable-load installations, and the system can be stalled without damage to the transmission or overload on the engine. In the case of power transmission between a tractor and a machine or between the engine and components of a self-propelled machine, there is little doubt that an hydraulic system is preferable to an electrical system. The latter is difficult to complete!) seal, is not so immune from damage, is not safe and generally does not have as high an efficiency. There is also the obvious advantage in that an hydraulic system can also be utilized to operate linear jacks for position control of individual parts of a machine. Hydraulic systems are not only trouble-free as long as the oil is kept clean, but they are also foolproof; this is not always true with an electrical system. Another advantage of the hydraulic over the electrical method is in the ease of effecting speed variation. In both cases, the speed of a motor can be varied by changing the speed of the engine and therefore of the pump or generator; this method is commonly used in the case of electrical transmission but has the disadvantage that the engine cannot be run at its optimum speed. With an hydraulic system, a variable-delivery pump can be used and the engine operated at constant speed; the equivalent electrical arrangements are less simple.
To permit variation of the speed of any one of a number of motors in the same system, it is necessary to insert a flow control valve in the line to each hydraulic motor, or a rheostat in the comparable electrical circuits. Although the latter may be less costly, the hydraulic arrangements for speed control are in general more suitable agricultural usage; further more, electrical systems usually require special arrangements for starting under load and must be specifically designed to withstand stall conditions.
Mechanical hydraulic electrical transmissions: This table compares general advantages associated with mechanical, pneumatic, hydraulic, and electrical means of producing linear mechanical motion.
Characteristics | Mechanical | Pneumatic | Hydraulic | Electric |
Complexity | very simple | simple | medium | high |
Peak power | high | medium | very high | high |
Size | medium | low | low | medium |
Control | gearbox | valves | valves | Electronic controller |
Accuracy | good | low | high | good |
Speed | medium | fast | low | fast |
Purchase cost | low | low | high | high |
Maintenance cost | low | low | high | low |
Total cost | low | low | high | medium |
Santiago Martinez – www.windydaysproducts.com
Mechanical hydraulic electrical transmissions chart
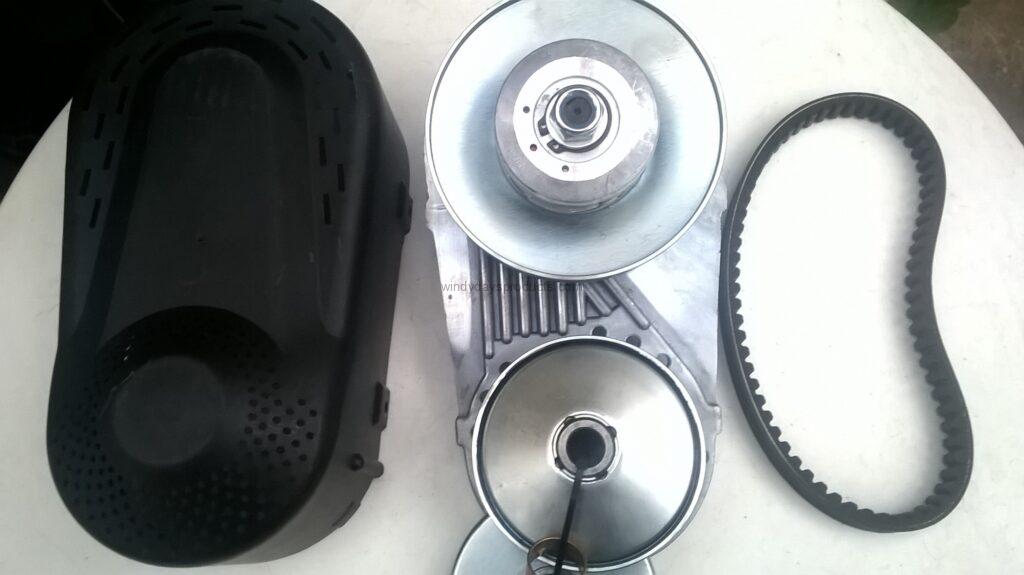
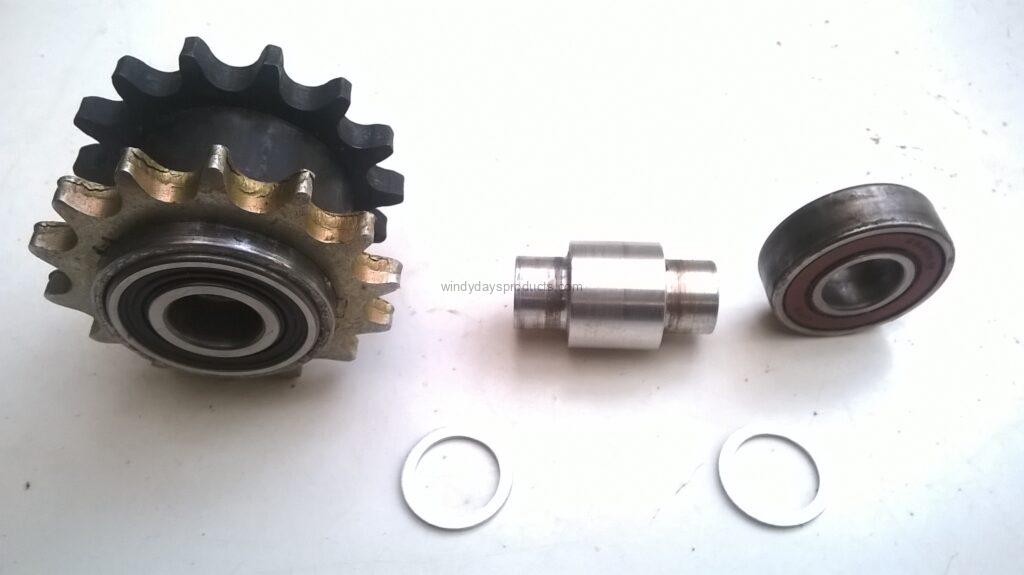
what about solar powered cars? can they be powered by hydraulic transmission ? or only electrics
eléctric vehicles are the future no matter the battery life